What is DLC?
◆ DLC is abbreviation of Diamond-Like Carbon, it also known as ‘amorphous carbon’.
◆ DLC coating has excellent properties for high hardness, abrasion resistance, corrosion resistance and chemical resistance. Until now, DLC applications have been used as alternatives to high hardness heat treatment. It is mainly used in tools. However, the scope of use of DLC coatings will gradually expand in the future.
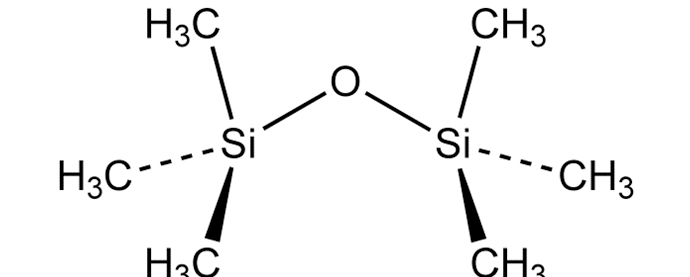
To improve the adhesion of the DLC coating layer, the residual stress generated by the DLC coating must be relieved.
To relieve residual stress, the buffer layer is should formed, and Select the appropriate buffer layer material based on the material of the product.
The materials used in the Buffer layer are Si, Ti, W, Cr, Fe, etc.
Tur-in Road Co., Ltd. has developed our own process to improve adhesion.
For example, HMDSO is used to form Si buffer layer.
We have secured a process that maximizes through HMDSO flow control.